JTAGテクニカルニュース vol.3
今回は、JTAGテストの色々なメリットをわかりやすくご説明します。
テスト手法と故障タイプ
JTAGテストは従来のテスト手法で困難なBGA/CSP実装ボードに対しての問題点を解決するツールとして各企業への導入が進んでいます。
図1は、従来のテスト手法とJTAGテスト手法で検出することのできる故障について図示したものです。
これを見ると、JTAGテスト単独でかなりのテスト故障が検出可能なことがわかります。
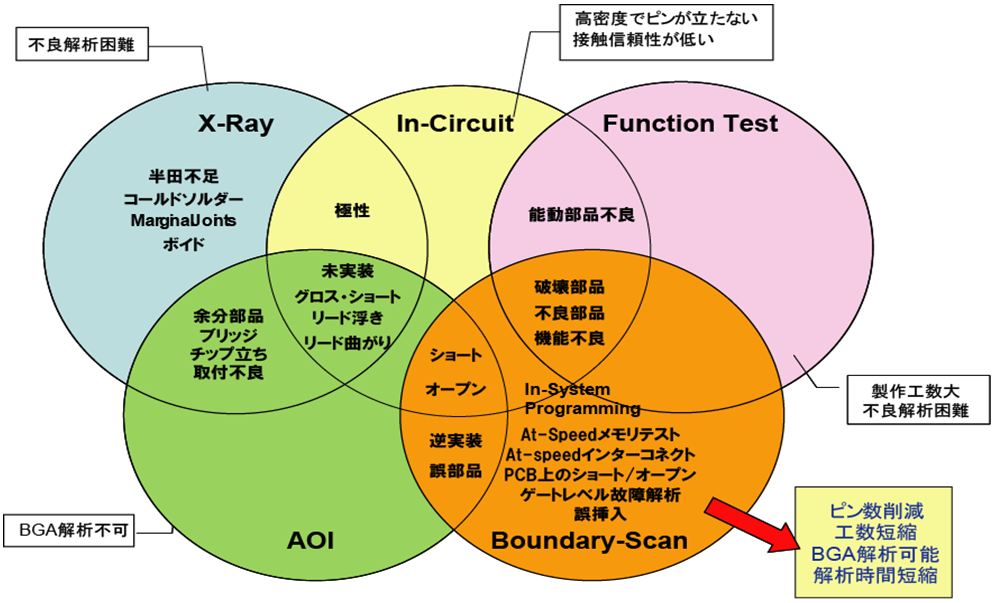
複合テストシステムへの期待
しかしながら、JTAGテストだけでは、従来のテストのメリットである部品定数の測定や機能チェックなどを行なうことが出来ないのも事実です。
そのため、テスト対象基板によっては、JTAGテストだけではなく、従来のテスト手法を併用した柔軟な「複合テストシステム」を構築することをお勧めいたします。
これによって、効率的かつ経済的なテストのシステムを実現することができます。
弊社からJTAGテストシステムをご導入いただいている企業様からも、このような「複合テストシステム」のお話が増えてきています。
それぞれのテスト手法のメリットを活かすことで、より高品質な製品を製造することができるのではないでしょうか?
製品開発サイクルごとのメリット
ICTやファンクションテストなどの従来手法のテストは、最終的な量産段階となった時点に基板形状やファームウェアが出来上がるため、 通常は、テストの実施も、この量産段階となります。
しかしながら、JTAGテストは、図2に示すように製品開発サイクルの各工程(開発/生産試作/量産)を通じてシームレスに使用することができ、 製品のTime to Marketを短縮することができる点が従来のテスト手法に比べて大きなメリットとなります。
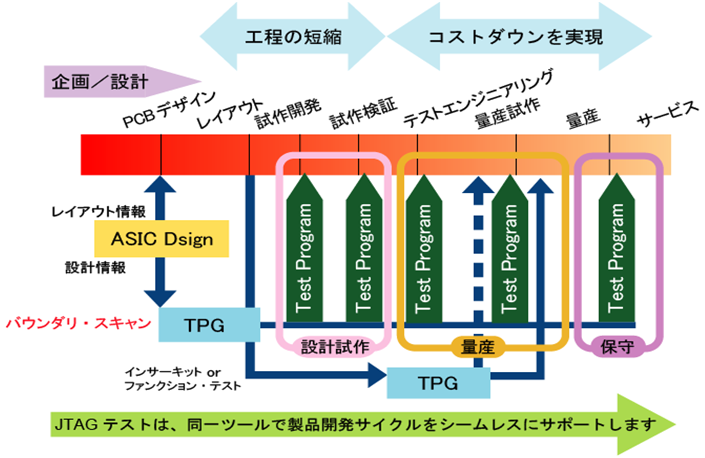
ここでは、JTAGテストに的を絞って、製品開発の各段階におけるメリットについて説明します。
研究開発段階におけるメリット
JTAGテストは、テスト対象基板のネットリスト(結線情報)とJTAGデバイス専用の電子ファイル『BSDLファイル』を基にテストデータを自動生成することができるため、 テストデータ作成のための工数が最小限で済みます。(図3テストフローご参照。)
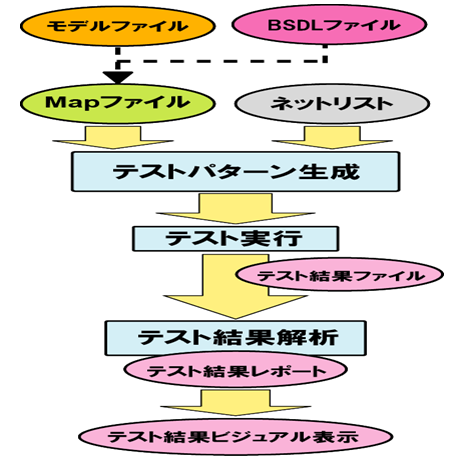
また、PCをホストとした非常にコンパクトなシステム環境でテストを行なえるため、 研究開発技術者は、試作品であっても不具合内容とその箇所を手元で容易に、そして迅速に特定することができます。
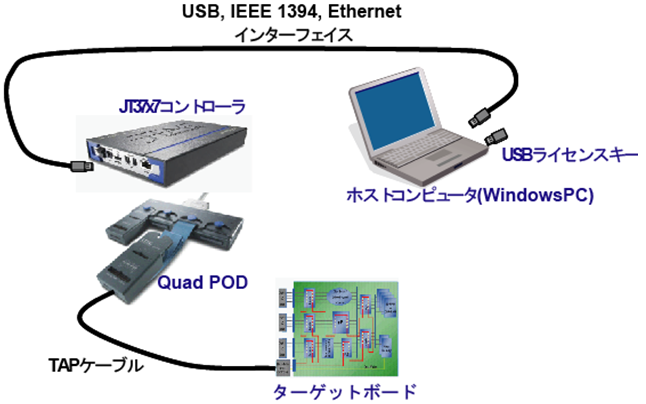
そのため、基板自体や実装に起因する不良による動作不具合に煩わされていた時間を削減することができ、本来の設計自体のデバックに専念することができます。
生産試作段階におけるメリット
JTAGテストを行なうためには、わずか5本のテスト制御線を基板上に実装すれば良く、 同一のネットリストであればレイアウトの異なる基板でも同一テストデータでテスト可能です。
また、同一回路で多機種に対応した基板の場合にも、機種ごとに異なる実装/未実装部品の情報を取り込むことにより、 それぞれの機種に対応したテストデータを簡単に生成することが可能です。
また、これまで難しかった生産試作段階における小ロット基板のテストが容易になり、生産技術者や研究開発技術者の工数が節減できます。
製品の量産段階におけるメリット
量産段階でJTAGテストを導入することにより、次のような効果が得られます。
【 技術面や時間に関するメリット 】
- 合否判定テストが高速にできる。
- 不良箇所の詳細な診断が可能なため、修理時間を短縮できる。
- 基板に詳しくないオペレータでも故障解析が容易にできる。
【 経営や経済面でのメリット 】
- テストシステムのコスト・パフォーマンスが高い。
- 基板ごとにネットリストとBSDLファイルを用意することで、汎用ツールとして使える。
- ピンプローブの削減やフィクスチャの多機種対応などにより、フィクスチャ製作費用が低減できる。
- 基板の不良検出により、高価な製品ボードの歩留まりが向上する。
- EMSに対して、製造・検査~修理をアウトソーシングできる。
- 製品の信頼性が向上する。